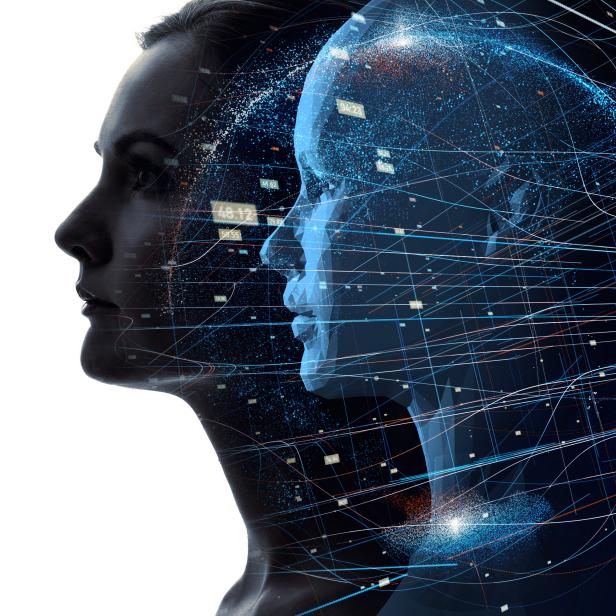
metamorworks
Digital Twins are a Virtual Replica of Everything
Imagine a world where every car or plane, every patient, every building, or even entire cities have their own virtual, real-time computerized replica--a digital double.
That concept is known as the digital twin and it could provide a way to measure, analyse, mend, and improve our lives in the real world.
‘If in doubt, clone it’ could be the mantra of the next generation of engineers, construction managers or doctors. More than just simulation, digital twins take information from internet-connected objects using sensors, software, and control systems–internet of things (IoT) devices. They measure data like temperature, position, air quality or speed to adapt and improve design or function.
For real-world entities like bridges, buildings and other large construction projects, this is hardly new. Engineers have used sensors and other devices to gather this information for decades. But the falling cost of IoT devices connected to the net allows digital twins to use data almost instantaneously to see the effects of changing conditions, and then make adjustments rapidly.
In construction, that means buildings become safer and cheaper to build because digital twins have access to real weather, structural and stress-point data. Bridges like the Queensferry Crossing in Scotland, for example, use water-level and wind speed threshold measurements to improve safety and manage traffic flow.
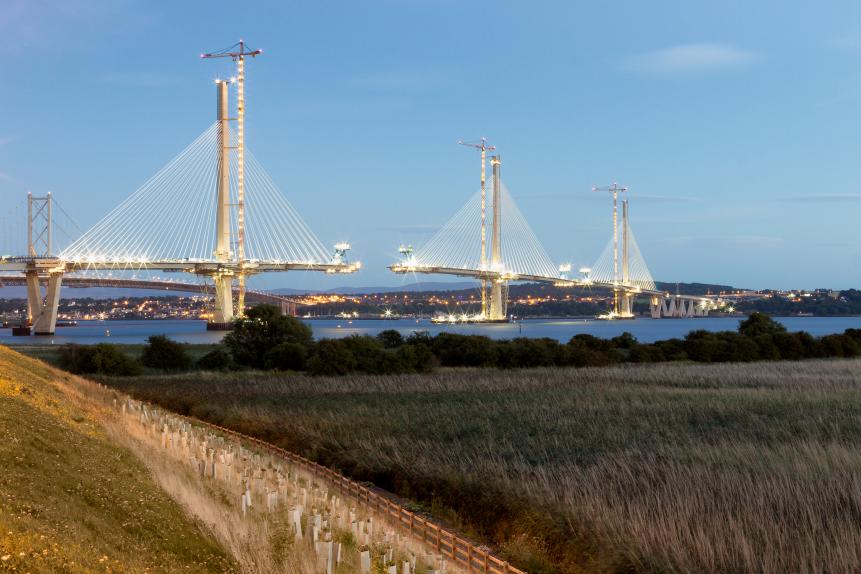
Steffen Schnur
Construction on the Queensferry Crossing road bridge.
Building systems such as heating, lighting and ventilation can also be automated and monitored remotely. Connected buildings then make smart cities, where buildings talk to one another and future performance can be predicted. In Australia’s state of Victoria, local government is building a digital twin of the entire state to transform urban planning and infrastructure builds, while the UK has a strategy to connect buildings and digital twins across the nation.
Manufacturing is another sector being disrupted by digital twin technology. Placing thousands of sensors throughout the production line allows companies to see how work is performed at each step of the process, systems efficiency and any bottlenecks. But it also allows different scenarios to be tested, such as how raw material shortages or price changes affect the business.
Boeing creates virtual replicas of its aircraft, systems and individual airplane parts–exact working models of each complex system and individual components. Its entire engineering and development system is digitized so engineers can call up the present status of any asset. Quality improvements of up to 50 per cent from twinning allowed Boeing to reduce costs and development time on air data equipment for its 777X twin-engine jet.
"I think this idea of maintaining a persistent set of computational models that are constantly being updated and evolved alongside a physical asset over its entire life cycle is really the essence of digital twins," said Michael Kapteyn, a researcher studying how scaling up digital twin computer models might handle a whole fleet of aerial drones.
The research team’s fixed-wing UAV was fitted with sensors and used to test instrument calibration and simulated flight damage. Its digital twin then used sensor information to assess the damage, predict how the UAV’s flight would be affected and recommend changes to allow it to continue safely. Ultimately, the goal is to expand the technology to handle other challenges, including fleets of aircraft, wind farm turbines or even heart patients.
And wind turbines are already benefiting from digital twin predictive data. An EU-backed design project has come up with a new foundation steel jacket for offshore wind turbines that reduces costs by 30 per cent. Another energy industry digital twin project in Australia helped model wildfire risk from vegetation touching power lines. Using aerial lidar and imagery data along with machine learning could reduce the amount spent by energy companies on trimming vegetation by up to 40 per cent.
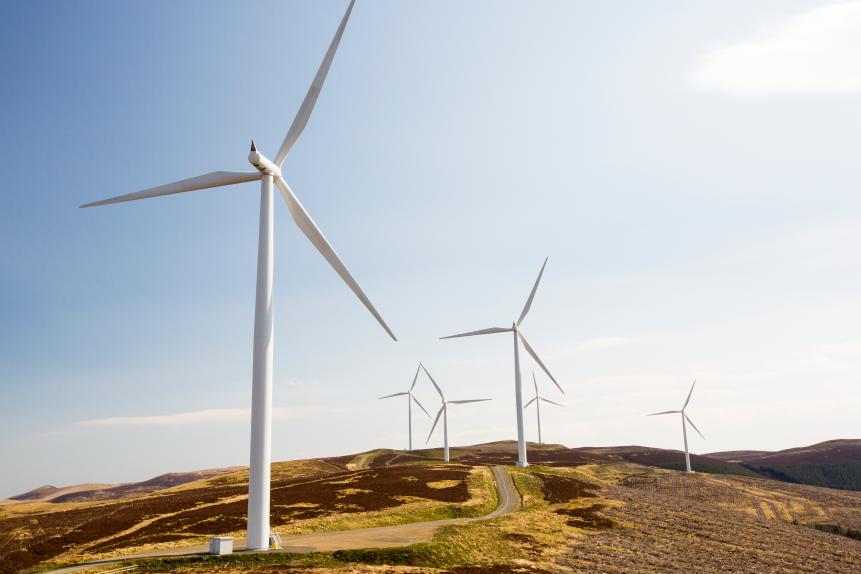
Ashley Cooper
Energy industry digital twins are helping to reduce the cost of wind turbines.
Where electrical grids become smart grids–using advanced software and smart meter feedback – energy company digital twins can model for renewable energy inputs and storage batteries. And then we’re closer to smart cities and responsive buildings that minimize impact on the environment.
Finally, in healthcare, the digital twin concept means creating computer models of disease or even a virtual human body. Personalized medicines or treatments could then be developed using a medical twin of each patient.
Filling in the blanks for individual organs using body data-linked digital models like Philips’ virtual heart or the Blue Brain Project is just the start. The idea of a medical twin that takes whole-person data from health trackers —including heart rate, blood pressure, breathing and other vital signs, and then advises on ways to improve our lifestyle could cut out health problems before they begin.