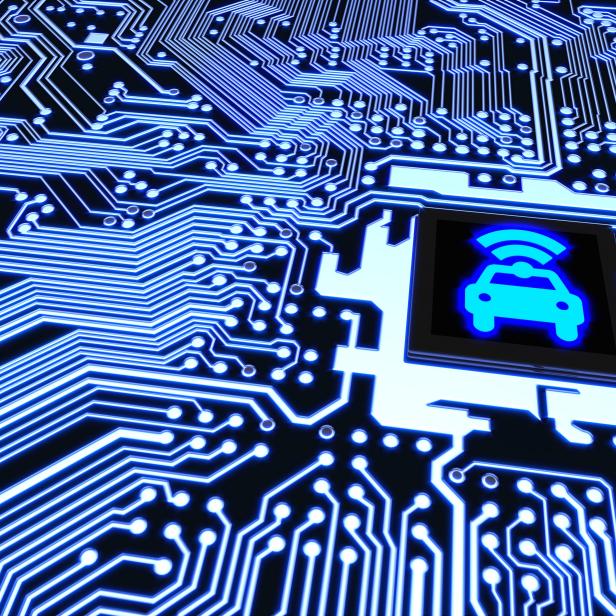
BeeBright
Car Industry Takes a Hit Due to Chip Shortage
Car manufacturers are facing an unpredictable future as a global shortage of computer chips, semiconductors, and rare earth metals affects traditional and electric vehicles. Large automotive factories have been forced to cut production at a time when a transition to electric models is expected to help fight climate change.
Chip shortfalls caused by high demand for personal computers, games consoles, and mobile devices during the pandemic added to supply chain disruption and the effects of a US-China trade war have left the auto industry struggling. Added to this, when demand for cars dropped during the coronavirus outbreak, the industry canceled orders, then found itself at the back of the queue of customers waiting for computer chips.
General Motors and Ford are two of the world’s largest car makers, but both stopped production entirely or cut shifts at their plants due to lack of chips. Auto giants like Volkswagen, Nissan, and Subaru plan to or have cut production as well. General Motors spokesperson David Barnas commented: “Semiconductor supply for the global industry remains very fluid.”
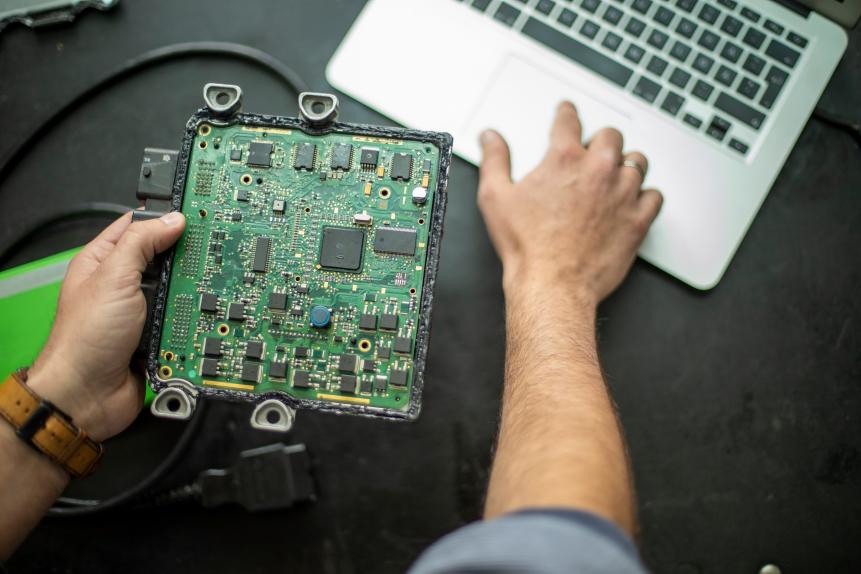
Nikola Ilic
Cars use microprocessors and other components in everything from engine management to automatic braking. But despite the inexpensive nature of many components used in making cars, the semiconductor shortage has compromised industry systems like ‘just in time’ manufacture. “The problem is, even if that 10-cent chip is missing, you can't sell your $30,000 car," said Gaurav Gupta, a semiconductor analyst at global research firm Gartner.
Electric vehicle (EV) specialists, Tesla, were also forced to temporarily close production lines at their Fremont plant in California because of parts supply problems. Chinese rival Nio believes the backlog in chip manufacturing will force the company to make fewer cars, despite increasing demand for EVs.
Analysts expect that EV batteries will be next in line to face component shortages, driving down electric car adoption rates over the next few years. Elements including lithium, nickel, cobalt, and carbon (in the form of graphite) are in short supply.
Tesla aims to build 20 million cars a year by 2030. To do that, it would need to use more than 30% of the world’s mined nickel and nearly double the world’s entire lithium supply based on current production output. Lithium has another problem, in that the amount of mining needed to provide electric cars to the world could wreak a terrible cost in habitat destruction, environmental damage, and pollution.
In the short term, the economic hit is the biggest problem, with one forecaster estimating that the automotive industry will lose $64 billion in sales while chip suppliers boost production to meet demand. In the longer term, mining issues will almost definitely affect adoption of EVs over combustion engine cars, making global emissions and climate change targets for transport harder to hit.
Car buyers should expect an increase in waiting times for some car models. On top of that chip, supplies for cell phones and laptops could be affected. While Apple and Samsung have the buying power to make sure they have priority, smaller brands may be more severely affected–meaning less choice and more expensive products.
Addressing shortages will take time. US President Joe Biden has signed an executive order to shore up supply chains by building microchip and semiconductor manufacturing plants, and securing domestic mineral supplies. Plans to invest heavily in EVs emphasize the need to be both climate-and worker-friendly, and preferably take place in the United States.